In the processing of medical injection molding molds, details determine success or failure. The following is a detailed elaboration on the processing ideas:
I. Parting Surface and Tolerance Settings
-
Parting Surface Considerations:
-
The parting surface of the rear mold should be determined based on the combined shape of two products to ensure accurate parting;
-
The parting surface of the front mold only needs to consider a single product, avoiding the use of the combined product parting surface to simplify the processing.
-
Tolerance Control:
-
The tolerance for the front and rear flanges is set at -0.05mm, and the tolerance for the spacing between the two flanges is ±0.02mm;
-
The clearance between the ejector pin and the ejector pin hole is 0.1mm on one side to ensure smooth ejection;
-
The tolerance for the center distance between the guide bushings and guide pins of the front and rear molds is ±0.01mm to ensure precise alignment of the mold;
-
Tolerances need to be added to the four sides and depth of the mold frame, especially with a negative tolerance of 0.02mm for the frame depth, to prevent burrs from occurring when the rear mold is rotated 180 degrees due to uneven height.
-
Mold Base Processing Benchmarks:
-
If the mold base has already been processed at the mold base factory, when processing the sprue bushing and ejector pin holes in our factory, the spacing center of the four guide pins and bushings should be used as the benchmark to avoid excessive deviations that could cause the mold to seize up.
-
When ordering the mold base, it should be specified as a two-color mold base to ensure that the four guide pins, bushings, and the frame are symmetrical, allowing the rear mold to match perfectly with the front mold after rotating 180 degrees.
-
Simplification of Rear Mold Rotating Two-Color Molds:
-
The two front mold cores are identical, with hard plastic injected on one side, then rotated 180 degrees (ensuring the product remains stable and the gate separates automatically), followed by soft plastic injection on the other side;
-
No ejector pins are needed on the hard plastic side, only on the soft plastic side;
-
Shrinkage needs to be carefully managed, with shrinkage placed according to how the hard and soft plastics intertwine.
-
Combination of Straight and 90-Degree Nozzles for Two-Color Molds:
-
For a two-color mold within one set of molds, a straight nozzle and a 90-degree nozzle can be used for plastic injection without the need for rotation, requiring only one mold core;
-
The separation of soft and hard plastics relies on shut-off positions.
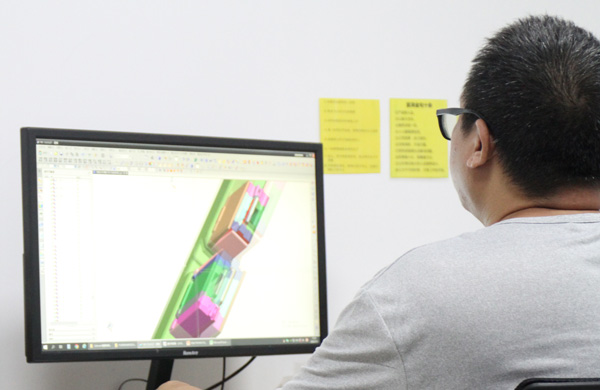
II. Mold Design and Processing Details
-
Mold Cavity and Core Design:
-
The two external shapes of the mold cavity are different, each forming a different product;
-
The two external shapes of the mold core are identical, facilitating processing and replacement.
-
Mold Fit Check:
-
The front and rear molds must fit perfectly when rotated 180 degrees around their center, and this check must be performed during design.
-
Ejector Pin Hole Layout:
-
The position of the ejector pin holes needs to be reasonably laid out, with a minimum spacing of 210mm;
-
For large molds, the number of ejector pin holes needs to be appropriately increased;
-
Extended ejector pins need to be designed in the mold, protruding about 150mm from the mold base plate, to accommodate the ejection requirements of the injection molding machine.
-
Rear Mold Base Design:
-
Two locating rings must be designed on the rear mold base plate to ensure stable positioning of the mold on the injection molding machine.
-
Front Mold Plate Thickness Requirements:
-
The total thickness of the front mold plate plus the A plate must be no less than 170mm, and relevant parameters of the injection molding machine need to be referenced for design.
-
Sprue Design:
-
The depth of the front side sprue should not exceed 65mm;
-
The distance from the top of the upper side (large gate) sprue to the center of the mold base should be no less than 150mm.
-
Design of the Second Injection Mold Cavity:
-
When designing the mold cavity for the second injection, consideration needs to be given to avoiding scratching the already molded product surface from the first injection;
-
Careful thought needs to be given to the strength of each shut-off position to prevent plastic deformation under high injection pressure, which could lead to burr formation.
-
Product Size Control:
-
The size of the product from the first injection molding can be slightly larger to ensure a tighter fit with the other mold cavity during the second molding, achieving a shut-off effect.
-
Slider Reset Issue:
-
Before the A and B plates are closed, it needs to be ensured that the front mold sliders do not reset first and damage the product;
-
If this issue exists, a design needs to be implemented to allow the A and B plates to close first, followed by the reset of the front mold sliders.
-
Cooling Water Layout:
-
The cooling water layout for the two mold cavities and the mold core should be sufficient, balanced, and consistent to ensure uniform cooling.
-
Injection Sequence:
-
In 99% of cases, the hard plastic part of the product should be injected first, followed by the soft plastic part, to avoid deformation of the soft plastic.
-
Impact of the Second Injection:
-
Attention needs to be paid to whether the flow of plastic during the second injection will impact the already molded product surface from the first injection, causing deformation;
-
If this possibility exists, measures need to be taken to improve it.
In summary, the processing of medical injection molding molds requires attention to detail, from parting surfaces, tolerance control, to mold design and processing details, as well as the importance of injection sequence. Each step needs to be carefully planned and executed to ensure the precision and stability of the mold, meeting the strict requirements of medical products.