In the process of medical mould manufacturing, parting is a crucial step. To ensure customer satisfaction, medical mould manufacturers must conduct a comprehensive analysis from multiple aspects before parting, including product characteristics, parting line design, parting surface selection, and the handling of kiss-off and shuttle surfaces. The following is a detailed analysis of these key dimensions:
I. Considerations for Plastic Product Characteristics
-
Appearance Surface Treatment: The appearance surface of plastic products is usually designed on the cavity side to ensure compliance with strict 2D tolerance controls, thereby presenting a exquisite appearance.
-
Product Retention Position: After mould opening, the product is generally retained on the core side, which helps improve production efficiency and mould durability.
II. Key Points for Parting Line Design
-
Definition of Parting Line: The line formed by the contact between the cavity and core sides is the parting line, which is usually the maximum outline of the product. For products with upper and lower covers, the parting line should be as consistent as possible to ensure aesthetic assembly.
-
Step Treatment: When the parting line has steps, frontal step differences should be avoided as much as possible. To this end, the core side needs to undergo glue relief processing, controlled within 0.05~0.1MM.
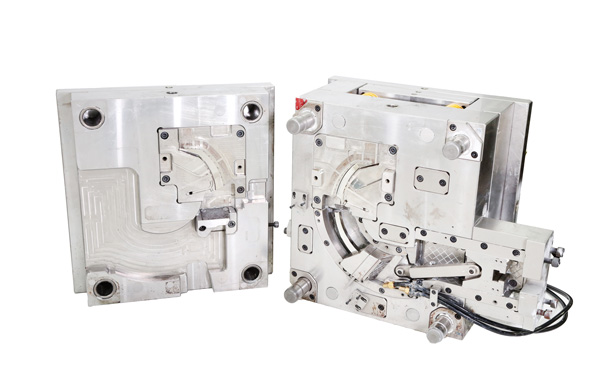
III. Principles for Parting Surface Selection
The parting surface is where the cavity and core sides meet, and its selection directly affects the processing difficulty of the mould and the moulding quality of the product. The optimal parting surface choices include planes, inclines, arcs, curves, and 3D surfaces, to ensure easy processing of the mould and product accuracy.
IV. Design Details for Kiss-off Surfaces
-
Hole Area Treatment: Areas with holes on the product need to be realized through kiss-off surfaces. The design of the kiss-off surface should ensure the accuracy and moulding quality of the hole positions.
-
Special Hole Type Treatment: For flare holes or mesh holes on the product, to prevent burrs on the kiss-off surface, one-third of the kiss-off surface should be designed on the cavity side, and two-thirds of the thickness on the core side. At the same time, the core side needs unilateral glue relief processing, controlled within 0.05~0.1MM.
V. Key Points for Shuttle Surface Design
-
Large and Medium-sized Moulds: For large and medium-sized moulds, to ensure mould life, the shuttle taper should be controlled within 3°~5°. This design helps reduce wear and damage to the mould during long-term use.
-
Small Connector Moulds: For small connector moulds, to control product tolerances and assembly accuracy, the shuttle taper can be designed within 0.2°~0.5°. This precise design helps ensure product stability and reliability.
In summary, medical mould manufacturers must comprehensively consider multiple factors before parting, including product characteristics, parting line design, parting surface selection, and the handling of kiss-off and shuttle surfaces. Through careful design and rigorous process control, high-quality medical mould products that meet customer needs can be ensured.