In the production process of injection mold factories, uneven surface brightness of medical injection molded products is a relatively common issue. This problem not only seriously affects the appearance quality of the products but may also have a negative impact on their overall quality and performance. So, how can we effectively solve this problem? In fact, we can take a series of targeted solutions from multiple aspects.
I. Precisely Adjust Injection Molding Parameters
-
Injection Speed Control
The injection speed has a significant impact on the surface gloss of medical injection molded products. If the injection speed is too fast, the material may stay in the mold cavity for too long, resulting in poor surface gloss of the product. At this time, the injection speed should be appropriately reduced. On the contrary, if the injection speed is too slow, the surface of the medical plastic part will not be dense enough, which will also lead to insufficient gloss. In this case, the injection speed should be appropriately increased to improve the surface density and gloss of the medical plastic part.
-
Melt Temperature Adjustment
The melt temperature is also a crucial factor. When the melt temperature is too low, the fluidity of the plastic part will be poor, which will affect its gloss. Therefore, the melt temperature should be appropriately increased to ensure good fluidity of the material and thus guarantee the gloss of the product surface.
-
Packing Pressure and Packing Time Optimization
Insufficient packing pressure or too short packing time will result in low density of the plastic part, which will ultimately affect the gloss. To solve this problem, the packing pressure should be increased and the packing time should be extended to fully compact the plastic part and improve its surface quality.
-
Cooling Time Control
For plastic parts with relatively thick walls, sufficient cooling is essential. If the cooling is not sufficient, the surface of the plastic part is prone to fuzzing, leading to a decrease in gloss. Therefore, the cooling system should be optimized to ensure uniform and sufficient cooling of the plastic part.
II. Comprehensively Optimize Mold Design and Manufacturing
-
Mold Temperature Management
The mold temperature has an important impact on the surface gloss of the product. If the mold temperature is too low or the cooling speed is too fast, a hard shell will easily form during the melt filling process, reducing the gloss. To this end, the surface temperature of the mold can be increased, the cooling speed can be reduced, or local heating can be applied at the mold gate to improve the melt filling effect.
-
Improve Mold Surface Finish
The roughness of the mold surface will directly affect the surface gloss of the product. To improve the mold surface finish, high - hardness materials should be used to manufacture the mold, and the mold surface should be carefully polished to ensure its smoothness.
-
Ensure Smooth Mold Venting
Poor mold venting will cause too much gas to remain in the mold cavity, forming bubbles or defects and affecting the surface gloss of the product. Therefore, the number, size, and position of the venting ports should be reasonably designed to ensure smooth mold venting and avoid the impact of gas on product quality.
-
Reasonably Design the Draft Angle
An improper draft angle of the mold will lead to difficult demolding or uneven force, which will affect the surface gloss of the product. Designing a reasonable draft angle can effectively reduce the resistance during the demolding process and ensure the smooth demolding of the product while avoiding scratches or deformations on the surface.
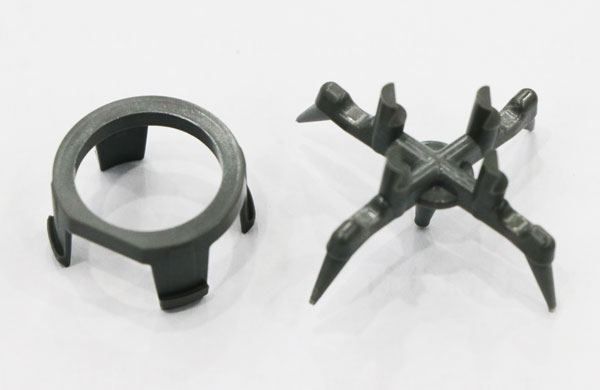
III. Strictly Improve Material Quality
-
Select High - Quality Plastic Materials
The quality of plastic materials plays a decisive role in the surface gloss of injection molded products. If the plastic material is uneven or contains a large number of bubbles and impurities, it will lead to poor surface gloss of the injection molded product. Therefore, high - quality plastic materials should be selected, and the materials should be fully pretreated to ensure their uniformity and purity.
-
Reasonably Add Additives
Adding an appropriate amount of heat stabilizers or gloss agents to the material can effectively improve the gloss of the product. Heat stabilizers can enhance the stability of the material and prevent it from decomposing during processing; gloss agents can improve the optical properties of the material surface and make the product surface brighter.
IV. Effectively Strengthen Equipment Maintenance
-
Regularly Clean Injection Molding Machines and Molds
Regularly cleaning and maintaining injection molding machines and molds is the key to ensuring that the equipment and molds are in the best condition. Cleaning can reduce the problem of decreased surface gloss caused by pollution and ensure stable product quality.
-
Ensure the Plasticizing Performance of the Screw
The plasticizing performance of the screw has an important impact on product quality. The plasticizing performance of the screw should be ensured to avoid quality abnormalities caused by poor plasticizing and thus ensure the smooth progress of the injection molding process and stable product quality.
In summary, solving the problem of uneven surface brightness of medical injection molded products requires comprehensive consideration of multiple aspects, including precise adjustment of injection molding parameters, comprehensive optimization of mold design and manufacturing, strict improvement of material quality, and effective strengthening of equipment maintenance. Through comprehensive measures, the surface gloss and overall quality of medical injection molded products can be significantly improved, providing strong support for the development of the medical industry.
Dongguan Yize Mold Co., Ltd. has been established since 2007 and has been rooted in Dongguan, the manufacturing capital, with convenient transportation and logistics advantages. Focusing on precision mold design and manufacturing and precision injection molding product production, the company integrates product design, precision mold manufacturing, injection molding and assembly, and after - sales service of automotive connectors, medical product injection molding, dust - free injection molding, and PFA custom injection molding into a complete solution. For relevant needs, please feel free to call +86 13302615729 (WeChat and Whatsapp available).