Introduction
In the field of medical devices, the quality and appearance of the housing are of utmost importance. They not only affect the overall quality of the product but also have a direct impact on the user's experience and trust. This article delves into the behind - the - scenes of large - scale injection molding for medical device housings, uncovering the secrets of this crucial manufacturing process.
Overview of Injection Molding
Definition and Principle
Injection molding is the process of injecting molten plastic into a mold to form a specific shape. For large - scale injection molding of medical device housings, due to their larger size, larger molds and higher pressure are required to ensure that the plastic fully fills the mold cavity and forms a complete and compliant housing.
Advantages
-
High Production Efficiency: Injection molding has extremely high production efficiency and can achieve rapid mass production. In the market where the demand for medical devices is increasing, this advantage ensures the timely supply of products to meet market needs.
-
Cost - Effectiveness: Large - scale manufacturing reduces the unit cost of the product. For medical device housings that require mass production, injection molding is a cost - effective choice, helping enterprises control costs and improve market competitiveness.
-
High Precision: Injection molding can achieve high - precision forming, ensuring product quality and assembly accuracy. In the medical device field, precise dimensions and shapes are crucial for product performance and safety, and the high - precision nature of injection molding can meet these strict requirements.
-
Ability to Achieve Complex Shapes: This process can easily create housings with complex shapes, meeting the diverse design needs of different medical devices. Whether it is a design with a unique appearance or a housing with a complex internal structure, injection molding can handle it.
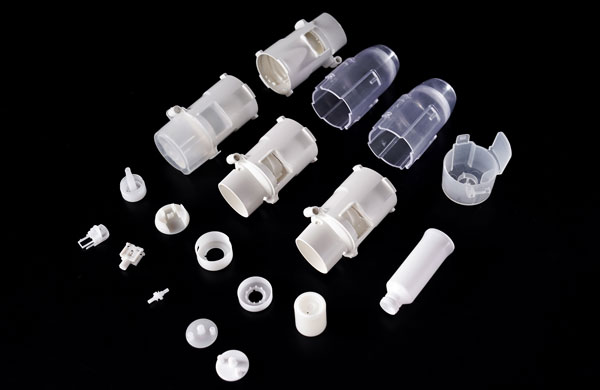
Material Selection for Medical Device Housings
Characteristics of Common Plastic Materials
-
ABS Material: It has good toughness and impact resistance, making it an ideal material for manufacturing medical device housings. In daily use, medical devices may be subject to various external impacts, and the ABS housing can effectively buffer these impacts and protect the internal precision components.
-
PC Material: It has higher strength and heat resistance and can withstand the high temperatures generated inside medical devices. For some medical devices that need to operate for a long time or have heating elements inside, the PC housing can ensure the stable operation of the equipment in high - temperature environments and extend its service life.
-
PP Material: It has good chemical resistance and insulation properties. In a medical environment, it may come into contact with various chemicals, and the PP housing can protect the medical device from corrosion in these environments. Meanwhile, its insulation properties can also ensure the safe use of the device.
Factors to Consider in Material Selection
When selecting materials for medical device housings, multiple factors need to be considered comprehensively. The product's usage environment is the primary factor, as different environments have different performance requirements for materials; performance requirements are directly related to product quality and function realization; cost factors determine the product's market competitiveness; and environmental factors are also receiving increasing attention in today's society. For example, if higher heat resistance and strength are required, PC material is a good choice; if cost and environmental friendliness are the focus, PP material is more suitable.
Process Flow of Large - Scale Injection Molding
Mold Design and Manufacturing
Mold design and manufacturing occupy a central position in large - scale injection molding for medical device housings. Mold design involves multiple aspects. The structural design must be accurate to ensure that the mold can precisely form the shape of the housing; the parting surface design should be reasonable to facilitate the smooth demolding of the product; and the cooling system design directly affects production efficiency and product quality. In the mold manufacturing process, advanced technologies such as numerical control are used to ensure the precision and surface quality of the mold, laying a solid foundation for subsequent injection molding.
Injection Molding Process
-
Heating and Melting: The plastic pellets are heated to a molten state, which is the first step in injection molding. Only when the plastic reaches an appropriate molten state can it be smoothly injected into the mold cavity.
-
Injection Filling: The molten plastic is injected into the mold cavity through the screw of the injection molding machine. During the injection process, parameters such as injection pressure, speed, and time need to be precisely controlled to ensure that the plastic fully fills the mold cavity and avoids problems such as short shots and flash.
-
Packing Stage: After the injection is completed, packing is required to prevent plastic shrinkage and defects. The packing process ensures that the plastic fully cools and solidifies in the mold, maintaining the shape and dimensional stability of the product.
-
Cooling and Solidification: The cooling stage is to cool and solidify the plastic in the mold to form the desired product shape. The cooling time directly affects product quality and production efficiency and needs to be adjusted reasonably according to the type of plastic and the size of the product.
-
Demolding: Finally, the product is removed from the mold through the demolding mechanism. Care should be taken during the demolding process to avoid damaging the product.
Post - Processing
The post - processing includes deburring, polishing, and painting. Deburring and polishing can effectively improve the appearance quality of the medical device housing, remove burrs and flaws on the product surface, and make the housing smoother and flatter; painting can give the housing various colors and decorative effects, enhancing the product's aesthetics and market competitiveness.
Quality Control and Inspection
Importance of Quality Control
Quality is the lifeline of an enterprise, and this is especially true in large - scale injection molding for medical device housings. Each product is related to the health and life safety of patients, so product quality must be strictly controlled to ensure that each product meets quality standards and customer requirements.
Methods and Means of Quality Control
-
Raw Material Inspection: Strict inspection of plastic pellets is carried out to ensure that their quality meets the requirements. Only high - quality raw materials can produce high - quality products.
-
Process Control: The injection molding process parameters are monitored and adjusted in real - time to ensure stable product quality. During the production process, any fluctuation in process parameters may affect product quality, so close attention and timely adjustment are required.
-
Finished Product Inspection: It includes appearance inspection, dimensional measurement, and performance testing to ensure that the product meets quality standards. Only through comprehensive inspection can qualified products be delivered to customers.
Common Quality Problems and Solutions
-
Shrinkage: Shrinkage is one of the common quality problems in injection molding for medical device housings, usually caused by uneven plastic shrinkage. It can be reduced by adjusting injection molding process parameters and optimizing mold design.
-
Deformation: Deformation may be caused by unreasonable mold design or uneven cooling. It can be solved by improving the mold structure and enhancing cooling.
-
Bubbles and Surface Defects: Bubbles and surface defects may be caused by moisture in the raw materials or improper injection molding process parameters. They can be solved by drying the raw materials and optimizing the injection molding process.