In the medical molding field, exquisite and durable plastic shells are crucial for ensuring the safety and functionality of equipment. However, during the injection molding process, due to various factors such as raw materials, injection molding machines, and molds, products may encounter a series of issues including brittleness, insufficient filling, warping, cracking, and bubbling. Today, Dongguan Yize Mold will delve into the strategies for addressing the brittleness issue in medical plastic shell injection molding, helping you enhance product quality and ensure that each item reaches its optimal state.
Strategies for Raw Material Optimization
-
Pressure Release and Treatment: For brittleness caused by insufficient release or treatment of internal stress in injection molded parts, annealing treatment is recommended. For nylon materials, soaking in warm water can accelerate stress release.
-
Material Compatibility: Reassess and redesign product structures to enhance the strength of weak areas, ensuring a perfect match between materials and product design.
-
Control of Recycled Materials: Limit the proportion of recycled materials and reduce their mixing with new materials to avoid performance degradation.
-
Impurity Removal: Rigorously screen raw materials, thoroughly clean the injection cylinder and material hopper, ensuring the purity of the plastic.
-
Quality Control of Recycled Materials: Carefully sort recycled materials, remove dust, and strictly follow the recycling process to ensure material quality.
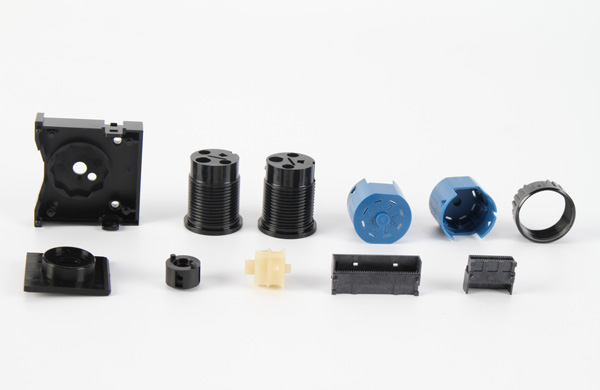
Adjustments for Injection Molding Machines
-
Melt Temperature Adjustment: Increase the temperature of the rear zone and nozzle of the injection cylinder, while adjusting the screw speed to ensure uniform plastic melting.
-
Prevention of Plastic Degradation: Comprehensively reduce the temperature of the injection cylinder, decrease back pressure, and use an injection cylinder with an exhaust function to ensure the integrity of the plastic molecular structure.
-
Increasing Filling Speed: By increasing mold temperature and maintaining stable cushion material, accelerate the mold filling speed to reduce the risk of brittleness.
Mold Optimization Measures
-
Mold Temperature Management: Appropriately increase mold temperature, limit the flow rate of cooling water, and ensure uniform mold surface temperature to reduce stress concentration during cooling.
-
Design of Runner and Gate: Adopt full-round runners and expand the size of runners and gates to lower the shear rate during mold filling, avoiding excessive destruction of plastic molecular chains.
About Us
Dongguan Yize Mold Co., Ltd., established in 2007 and rooted in the manufacturing hub of Dongguan with convenient transportation and logistics networks, specializes in precision mold design and manufacturing, as well as precision injection molding production. Our services cover multiple fields including automotive connectors, medical product injection molding, dust-free injection molding, PFA custom injection molding, and more, providing one-stop solutions from product design, mold manufacturing, injection molding, and assembly to after-sales service. Welcome to call us at +86 13302615729 (WeChat, WhatsApp same number) to discuss your project needs and create a better future together.
Through the implementation of these comprehensive strategies, we believe you can effectively solve the brittleness issue in medical plastic shell injection molding, enhance product quality, and win market trust.