Introduction
In the medical field, the quality of precision medical device injection - molded products is closely related to patients' health and the effectiveness of medical treatments. However, the production process faces numerous challenges. From the selection of raw materials to mold manufacturing, from the adjustment of process parameters to environmental control, and to quality inspection and feedback, each link requires meticulous management. The following is an in - depth analysis of how to effectively ensure the product quality.
How to Control Product Quality in Precision Medical Device Injection Molding
Raw Material Quality Control
Material Selection Criteria
The selection of materials for precision medical device injection molding needs to consider multiple factors to ensure that the materials are suitable for their functions and usage environments.
-
Biocompatibility: The materials must not cause adverse reactions when in contact with the human body. For example, implantable devices require highly biocompatible materials to ensure long - term safety after implantation.
-
Chemical Stability: They should be able to resist various chemical substances in the medical environment, preventing chemical reactions that could degrade the material's performance and affect the quality of the device.
-
Physical Properties:
-
Strength: The appropriate strength material should be selected according to the stress condition of the device. For instance, surgical instruments need to be resistant to breaking, and implantable devices must withstand the stress of the human body.
-
Elastic Modulus: For materials like vascular stents, the elastic modulus should match that of human blood vessels to ensure proper support and compliance.
-
Thermal Stability: The temperature changes during injection molding and use, such as high - temperature sterilization, should be considered. The material should not deform under such conditions.
Supplier Screening and Management
-
Key Indicators for Evaluating Suppliers:
-
Production Qualification: The supplier should have legal production licenses and quality certifications.
-
Quality Control System: There should be a well - established process to ensure product quality.
-
Industry Reputation: Refer to peer evaluations to select suppliers with a good reputation.
-
Establishing Long - term Cooperative Relationships:
-
Stability: Ensure the stability of the supply quantity and delivery time of raw materials.
-
Quality Consistency: Help suppliers deeply understand the requirements to ensure consistent quality.
Raw Material Inspection Process
Raw materials entering the factory need to undergo comprehensive and strict inspections.
-
Appearance Inspection: Observe the color, transparency, and the presence of impurities to make a preliminary judgment on the quality.
-
Physical Performance Testing:
-
Density: Measure the density to determine the composition and check for doping.
-
Hardness: Understand the wear - resistance and compression - resistance properties.
-
Chemical Performance Analysis:
-
Component Analysis: Confirm that the chemical composition meets the standards.
-
Purity Detection: Ensure the purity of the material to guarantee the performance and safety of the device.
-
Testing of Properties Related to the Injection Molding Process:
-
Flowability: It affects the injection molding process. Select materials with appropriate flowability according to the product requirements.
-
Shrinkage Rate: Improper control of the shrinkage rate can lead to size deviations of the product. Choose materials with a suitable shrinkage rate.
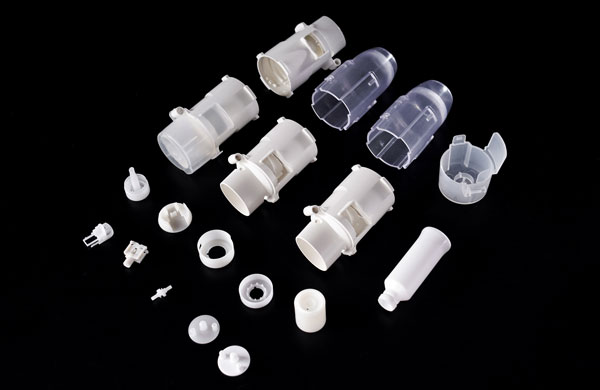
Quality Assurance of Mold Design and Manufacturing
High - Precision Mold Requirements
Precision medical device injection molding has strict requirements for mold precision, which is crucial for the quality of the injection - molded products.
-
Cavity Dimension Precision: It needs to reach the micron or even nanometer level. Slight deviations can affect the product size and the performance of the medical device, such as in the case of micro - components molds.
-
Surface Finish: The surface of precision medical molds should be smooth, which is conducive to the uniform flow of the melt, avoiding surface defects on the product and improving the appearance quality, such as in the case of wearable device shells.
-
Ejection Mechanism Design: Carefully design the ejection mechanism to ensure that complex and high - precision products can be ejected smoothly without damage, such as thin - walled or precision - structured injection - molded parts.
Mold Manufacturing Processes and Technologies
Advanced processes and technologies are used to meet the high - precision requirements of molds.
-
Electrical Discharge Machining (EDM): By generating pulsed electrical discharges between the electrode and the workpiece to erode the metal, it can precisely control the machining dimensions and create complex cavities to meet the precision requirements of special - shaped molds.
-
Numerical Control (NC) Machining: Use NC programs to control the movement of machine tools for high - precision machining of mold components, ensuring consistent precision in batch production and guaranteeing product quality.
-
Precision Grinding: Perform fine grinding on key parts of the mold to improve the surface finish, allowing the melt to flow smoothly and reducing surface defects on the product.
Mold Verification and Maintenance
Molds need to be strictly verified and maintained before and after being put into production to ensure product quality.
-
Trial Molding: Conduct actual injection molding to test the mold performance and product quality. If the requirements are not met, adjustments and improvements should be made.
-
Product Dimension Measurement: Compare the actual dimensions of the trial - molded products with the design dimensions. Analyze the causes of deviations and take corresponding measures.
-
Appearance Inspection: Check the appearance of the trial - molded products for defects and solve the problems in a targeted manner.
-
Mold Maintenance During Use:
-
Cleaning: Regularly clean the mold to remove impurities, ensure good heat dissipation, and maintain product quality.
-
Lubrication: Lubricate the moving parts to reduce wear and extend the service life of the mold, ensuring smooth ejection.
-
Replacement of Worn Parts: Replace worn parts in a timely manner to maintain the precision and normal operation of the mold.
Precise Control of Injection Molding Process Parameters
Key Process Parameters
In precision medical device injection molding, these key process parameters affect product quality.
-
Injection Pressure: If the pressure is too high, it may cause flash, overflow, etc.; if it is too low, it may lead to insufficient filling, both of which will affect product quality.
-
Injection Speed: If the speed is too fast, it is easy to trap air and form bubbles; if it is too slow, the viscosity of the melt will increase, making filling difficult.
-
Holding Time: The length of the holding time affects the product's density, dimensional accuracy, and internal quality. If the holding time is too short, there may be sink marks and other problems; if it is too long, it will increase internal stress.
-
Cooling Time: Insufficient cooling time can cause product deformation and size instability; although a longer cooling time can fully solidify the product, it will affect production efficiency and product performance.
-
Mold Temperature: An appropriate mold temperature helps the melt flow uniformly. If the temperature is too high or too low, it will affect the product's molding quality.
Parameter Optimization and Setting
It is necessary to precisely optimize and set the process parameters to ensure product quality.
-
Design of Experiments (DOE): By systematically changing multiple parameters and observing their effects on product quality, determine the optimal parameter combination.
-
Simulation Analysis Software (such as Moldflow): Use the software to simulate the injection molding process, predict problems, and adjust parameters accordingly to optimize product quality.
-
Combining Product Characteristics and Material Properties: Different product structures and material properties require corresponding adjustments to the process parameters.
Real - time Monitoring of Process Parameters
-
Monitoring Equipment and Technologies: Equip with temperature, pressure sensors, and data acquisition systems to keep track of the process parameters in real - time.
-
Discovery of Abnormalities and Adjustment Measures: If abnormal fluctuations in the parameters are detected, immediate adjustment measures should be taken to ensure product quality.
Strict Control of the Production Environment
Cleanliness Requirements
-
Different Grade Standards: Precision medical device injection molding requires different cleanroom standards according to the type of device and the production process. For example, implantable devices have higher cleanliness requirements.
-
Importance of a Clean Environment: A clean environment can prevent impurities from mixing into the product, ensuring the product's biocompatibility and safety. Even a small amount of contamination can lead to serious consequences.
Temperature and Humidity Control
-
Effects on Materials and Molds: Temperature and humidity affect the performance of injection - molding materials and the condition of the mold. High temperature may cause material deformation, affecting product quality; low humidity can easily generate static electricity and attract impurities. Inappropriate temperature and humidity can also cause the mold to deform or rust.
-
Control Measures: Use air conditioners to adjust the temperature, dehumidifiers to reduce humidity, and equip with temperature and humidity sensors for real - time monitoring and timely adjustment.
Static Electricity Protection
-
Hazards of Static Electricity: Static electricity discharge can damage the electronic components of the product, attract impurities, and affect the product's function, appearance, and biocompatibility.
-
Protective Measures: Install static eliminators to neutralize static electricity, use anti - static materials to make tooling and fixtures, and require workers to wear anti - static clothing to prevent the impact of static electricity on the product.
Quality Inspection and Feedback Mechanism
Multi - dimensional Quality Inspection
-
Appearance Inspection: Visually inspect the surface of the injection - molded products for scratches, bubbles, flow marks, and other defects, which can affect both the appearance and user experience. Detailed inspections should be carried out at all stages of production.
-
Dimension Measurement: Compare the actual dimensions of the product with the design dimensions. Slight deviations may lead to assembly difficulties or affect product performance. Precise tools should be used to strictly measure key dimensions.
-
Performance Testing:
-
Mechanical Performance Testing: Test the strength, hardness, toughness, etc., of the product to ensure that surgical instruments and other devices are safe and reliable when subjected to external forces.
-
Biocompatibility Testing: Evaluate the product's reaction in the human body environment to ensure that it is harmless to humans.
-
Chemical Stability Testing: Test the product's stability after contact with chemical substances to ensure the safety and effectiveness of the medical device.
Online Detection Technology
-
Optical Detection: Use optical principles to monitor the product's surface and dimensions in real - time, which can quickly detect problems such as scratches, bubbles, and size deviations.
-
Ultrasonic Detection: By emitting and receiving ultrasonic signals, analyze the internal situation of the product to detect defects such as voids and inclusions, which is suitable for complex products.
-
Advantages of Online Detection: It can detect quality problems in real - time and provide feedback in a timely manner, reducing costs and waste, and facilitating the optimization of the production process to improve production efficiency and quality.
Quality Feedback and Continuous Improvement
-
Quality Feedback Mechanism: Promptly feed back the inspection results to relevant departments. For example, appearance problems are fed back to the production department, and size deviations are fed back to the process department for timely problem - solving.
-
Continuous Improvement: Based on the feedback information, optimize raw materials, molds, process parameters, etc. For example, re - select materials, repair molds, and optimize parameters to steadily improve product quality.
Summary
In summary, to control the quality of precision medical device injection - molded products, meticulous attention must be paid to every link, from raw materials, molds, process parameters, the production environment, to quality inspection and feedback. Only through multi - faceted strict requirements and continuous optimization and improvement can we ensure high - quality products that meet the high standards of the medical industry, safeguard patients' health, and promote the steady development of the industry.
Dongguan Yize Mold Co., Ltd. was founded in 2007, with its headquarters in Dongguan, the manufacturing capital of China, enjoying convenient transportation and logistics. The company has been engaged in precision mold design and manufacturing and precision injection - molded product production for many years, focusing on a complete set of solutions including product design, precision mold manufacturing, injection molding and assembly, and after - sales service for automotive connectors, medical products injection molding, dust - free injection molding, and PFA custom injection molding. Welcome to inquire by calling +86 13302615729 (also available on WeChat and Whatsapp).