With the rapid development of minimally invasive medical technologies, guidewire catheters—as core components of interventional devices—directly impact clinical surgical outcomes through their precision, reliability, and production efficiency. This article dissects a one-stop solution for guidewire catheter manufacturing, covering medical-grade material development, precision injection molding innovation, and integrated digital management. By addressing bottlenecks in mass production and compliance, it empowers medical device enterprises to achieve breakthroughs in efficiency and regulatory compliance.
1. Medical-Grade Material Selection & Precision Injection Molding Breakthroughs
-
Biocompatibility Standards: Guidewire catheters in contact with human tissues must pass ISO 10993 biocompatibility tests (cytotoxicity ≤ Grade 1, no sensitization reactions). Recommended materials include medical-grade PEEK (polyetheretherketone) and modified PPSU (polyphenylsulfone), which balance high strength with X-ray translucency.
-
Material Modification Techniques: Barium sulfate nanoparticles are added for radiopacity enhancement, while PEEK toughness is improved through blend modification (elongation at break increased from 35% to 68%), reducing in-surgery fracture risks.
-
Ultra-Thin Wall Injection Molding: For 0.2mm-thick catheter structures, valve-gate hot runner systems and high-pressure clamping achieve uniform filling (tolerance ±0.01mm), eliminating defects like flash and sink marks.
-
Gas-Assisted Injection Molding & Insert Molding: Nitrogen-assisted molding reduces internal stress, while titanium alloy needle tips are overmolded for enhanced puncture performance (tip hardness HRC 58-62), meeting neurointerventional surgery demands.
2. Digital Tooling & Intelligent Production Integration
-
AI-Driven Mold Optimization: Finite element analysis (FEA) simulates stress distribution during catheter puncture, optimizing parting lines and draft angles. Trial molds are reduced from 12 to 3, shortening development cycles by 40%.
-
Mold Health Monitoring: Strain sensors embedded in mold cavities monitor fatigue in real-time, with machine learning predicting mold lifespans and cracking risks 3 months in advance.
-
Medical-Grade Cleanroom Production: Class 100,000 (ISO 8) cleanrooms with FFU (fan filter units) and positive pressure systems control airborne particles ≤0.5μm/m³, meeting ISO 14644-1 standards.
-
Online Defect Detection: Machine vision modules with AI algorithms detect surface defects (scratches, burrs) at 0.02mm precision, achieving a 99.7% rejection rate for non-conforming parts.
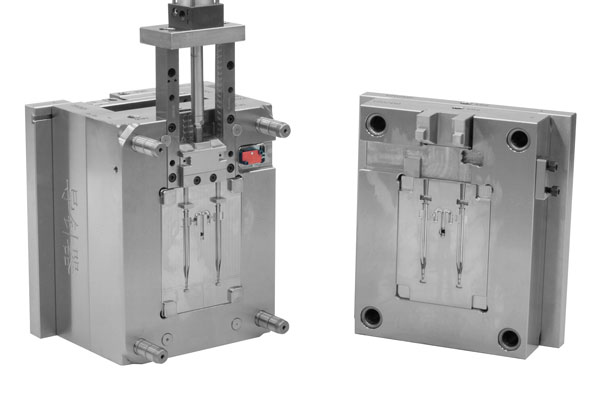
3. Full-Chain Compliance & Cost-Efficiency Strategies
-
Medical Quality Control Systems: Process validation (PV) and risk assessments comply with ISO 13485, generating DMF (device master files) and DOE (design of experiments) reports to shorten FDA 510(k) approval by 6 months.
-
Traceability Systems: RFID chips record injection parameters, material batches, and inspection data for end-to-end traceability.
-
Scalable Production Cost Control: Modular mold designs split catheters into three modules (needle body, handle, positioning ring), enabling daily 3-batch switches via quick mold change (QMC) systems and boosting efficiency by 55%.
-
Energy & Material Optimization: Servo-driven injection machines and closed-loop temperature control reduce energy use by 22%; customized pellets developed with suppliers increase material utilization from 82% to 91%.
4. Industry Practice: One-Stop Solution Implementation
Case Study: Neurointerventional Device Enterprise: Precision molding and biocompatible material validation optimized puncture force consistency from ±15% to ±3%, raising clinical success rates by 21%. Post-mass production, unit costs dropped by 38%, and annual capacity exceeded 2 million units, becoming the first domestic guidewire catheter supplier to pass FDA 510(k) certification.
Environmental Benefits: Biodegradable PBS injection molding replaced traditional PVC, cutting carbon emissions by 42% and aligning with EU MDR (Medical Device Regulation) green manufacturing requirements.
5. Future Trends: Intelligent Medical Devices & Green Production
-
AI-Assisted Customization: CT imaging data and 3D printing enable personalized guidewire catheters for complex vascular anatomies.
-
Recyclable Medical Materials: Development of medical-grade rPEEK (recycled PEEK) injection molding reduces carbon footprints by 35%, responding to global medical device carbon certification trends (e.g., EPD).