Medical laryngoscopes, as critical tools for clinical diagnosis, require their injection-molded components to meet stringent standards for precision, biocompatibility, and chemical stability. Defects occurring during the injection molding process can directly impact product safety and functionality. Drawing from research findings in the field of medical device injection molding, this article provides an in-depth exploration of common defects in injection-molded medical laryngoscope components and their corresponding solutions.
1. Typical Defects in Injection-Molded Medical Laryngoscope Components
-
Flash (Burrs)
-
Appearance: Thin plastic residues appear at the edges or parting lines of the laryngoscope housing, potentially causing scratches to operators or affecting packaging seal integrity.
-
Causes: Insufficient mold clamping accuracy, inadequate clamping force, or excessive injection pressure leading to melt overflow.
-
Case: Flash on the edges of syringe barrels once caused risks of plastic debris detachment during medical operations.
-
Sink Marks
-
Appearance: Localized depressions occur on the surface of transparent laryngoscope components (e.g., observation windows), affecting light transmittance and structural strength.
-
Causes: Uneven wall thickness causing differential cooling shrinkage or insufficient holding pressure during the packing phase.
-
Case: Shrink marks on infusion set drip chambers once led to reduced strength, affecting fluid flow observation.
-
Weld Lines
-
Appearance: Linear marks form at the junctions of multiple melt flows on the laryngoscope housing, potentially becoming sites for bacterial growth.
-
Causes: Poor gate design or excessively slow injection speed leading to uneven cooling of melt fronts.
-
Case: Weld lines on hemodialyzer casings once sparked controversies over infection risks.
-
Warpage
-
Appearance: Distortions occur in the laryngoscope handle or lens supports, affecting assembly precision and operational stability.
-
Causes: Uneven cooling causing differential shrinkage rates or improper ejection methods inducing internal stresses.
-
Case: Warpage in medical petri dishes once led to abnormal distribution of internal liquids.
-
Insufficient Chemical Stability
-
Appearance: Laryngoscope components swell or release harmful substances upon contact with disinfectants.
-
Causes: Improper material selection or contamination during the injection molding process.
-
Case: Reactions between drug vial materials and specific medications once caused drug contamination incidents.
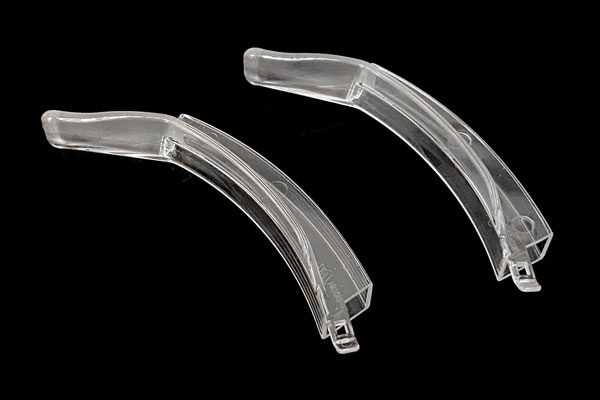
2. Systematic Analysis of Defect Causes and Solutions
-
Mold Optimization and Process Parameter Adjustment
-
Flash Control: Improve mold clamping accuracy and use high-rigidity templates; reduce injection pressure and optimize packing time.
-
Sink Mark Elimination: Add cooling channels in thick-walled areas and adjust packing curves to compensate for shrinkage.
-
Weld Line Improvement: Optimize gate locations and numbers, adopting multi-point gating designs; increase mold temperature to enhance melt fluidity.
-
Material Selection and Pre-treatment
-
Biocompatibility: Choose medical-grade plastics compliant with ISO 10993 standards, avoiding materials containing harmful additives like phthalates.
-
Chemical Resistance: Select materials resistant to chemical corrosion, such as polycarbonate (PC) or polysulfone (PSU), for disinfectant environments.
-
Drying Treatment: Pre-dry hygroscopic materials (e.g., PA, PC) to prevent silver streaks or bubbles caused by moisture.
-
Refined Control of Injection Molding Process
-
Temperature Management: Segmentally control barrel temperatures to avoid material accumulation at the nozzle; increase mold temperature to reduce melt front cooling.
-
Pressure Control: Implement multi-stage packing strategies, dynamically adjusting pressures based on product wall thickness; prevent melt backflow caused by worn screw non-return valves.
-
Speed Optimization: Use high-pressure low-speed injection for thin-walled components to prevent melt fracture; increase injection speed for thick-walled components to reduce cooling time differences.
-
Quality Inspection and Process Validation
-
IQ/OQ/PQ Validation: Complete Installation Qualification (IQ), Operational Qualification (OQ), and Performance Qualification (PQ) before mass production to ensure stable process parameters.
-
Dimensional Accuracy Control: Use coordinate measuring machines to inspect critical dimensions and establish correlation models between mold temperature and shrinkage rates.
-
Chemical Stability Testing: Simulate actual usage environments to test interactions between materials and disinfectants, ensuring no release of harmful substances.
3. Future Directions for Injection Molding of Medical Laryngoscopes
With the trend toward miniaturization and integration of medical devices, injection molding processes need to further advance in precision and efficiency. For example, microcellular injection molding technology can reduce sink marks, while hot runner systems in molds can optimize melt filling uniformity. Additionally, the application of artificial intelligence in process parameter optimization (e.g., defect prediction models based on machine learning) will become key to enhancing quality stability.
Conclusion
Resolving injection molding defects in medical laryngoscopes requires collaborative optimization across mold design, material selection, process parameters, and quality inspection. Through systematic analysis of defect causes and integration of industry best practices, product safety and reliability can be significantly improved, providing solid guarantees for clinical applications.