In medical injection molding, product whitening is a common surface defect characterized by white marks or brightened areas on molded parts after ejection, severely impacting aesthetics and functionality. This issue is particularly critical in high-precision medical devices, where whitening can lead to product rejection or customer complaints. This article analyzes the root causes of whitening in medical injection molding and proposes systematic solutions tailored to its unique requirements.
1. Causes of Whitening
Whitening stems from internal stress concentration in the material during molding, often triggered by:
-
Excessive ejection force: High-rigidity medical-grade plastics (e.g., PC, PPSU, PEEK) are prone to surface damage under uneven or high-speed ejection.
-
Mold design flaws: Poor ejector pin layout, uneven mold temperature, or improperly sized gates.
-
Uncontrolled process parameters: Over-packing pressure, prolonged holding time, or insufficient cooling.
-
Material-mold mismatch: Rough mold surfaces exacerbate friction during demolding.
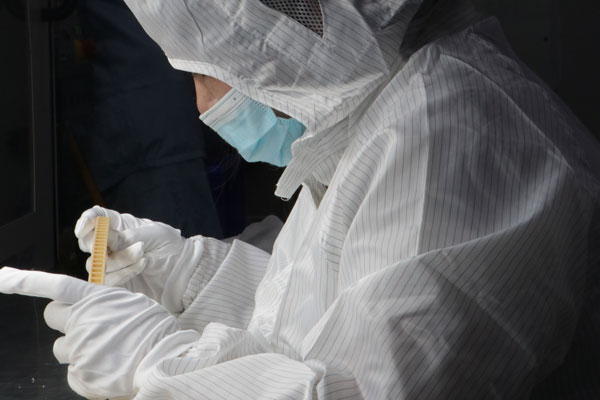
2. Systematic Solutions
a. Mold Design Optimization
-
Ejector system refinement: Increase pin quantity, adopt flat-tip pins or sleeve ejectors, and implement staged ejection for deep cavities.
-
Precision mold temperature control: Use zoned temperature systems to minimize thermal gradients, critical for transparent medical components.
-
Gate/runner optimization: Replace direct gates with submarine or pinpoint gates to reduce flow-induced stress.
b. Process Parameter Adjustment
-
Multi-stage packing: Balance cavity filling and shrinkage compensation to avoid over-packing.
-
Velocity profiling: Use "slow-fast-slow" injection for thin-walled parts to limit shear heating.
-
Ejection speed reduction: Lower speeds to 0.5–1.0 m/s and integrate pneumatic/hydraulic buffers.
c. Material and Surface Treatments
-
Additive modification: Incorporate lubricants (e.g., silicone powder) or toughening agents to reduce friction.
-
Mold surface finishing: Achieve ultra-smooth surfaces (Ra ≤ 0.05 μm) via polishing or PVD coatings.
d. Real-Time Monitoring and Prevention
-
Deploy IoT-enabled presses to track critical parameters (e.g., pressure, temperature) with automated alerts.
-
Implement regular mold maintenance to prevent ejector pin blockages or hot runner clogging.
3. Case Study: Whitening in Medical Catheter Connectors
A PC catheter connector exhibited whitening due to insufficient ejector pins (2 pcs) and misaligned positioning. Solutions included:
-
Adding 2 pins symmetrically aligned with ribs.
-
Reducing packing pressure from 120 MPa to 90 MPa and extending cooling by 5 seconds.
-
Hard chrome plating the cavity (Ra 0.03 μm).
Result: Defect rate dropped from 8% to 0.2%.
4. Conclusion
Addressing whitening in medical injection molding requires integrated improvements in mold design, process control, material selection, and monitoring. Digital tools like mold flow simulation and smart manufacturing systems will be key to meeting escalating precision demands.