In the medical industry, injection molding technology is a cornerstone for manufacturing high-precision, high-performance medical devices. From disposable syringes to implantable stents, and from surgical instruments to diagnostic equipment housings, the safety and functionality of medical injection-molded products directly depend on material selection. This article systematically reviews commonly used materials in medical injection molding, analyzing their properties, applications, and future trends to provide insights for industry practitioners.
1. Core Requirements for Medical Injection Molding Materials
Medical products interact directly with the human body or are used for life support, so materials must meet three key standards:
-
Biocompatibility: Certified by ISO 10993 or USP Class VI to ensure no cytotoxicity or sensitization.
-
Chemical Stability: Resistant to sterilization and corrosion, avoiding harmful substance release under high temperatures, radiation, or chemical agents.
-
Processability: Flowability and shrinkage rates must align with precision injection molding to ensure dimensional accuracy.
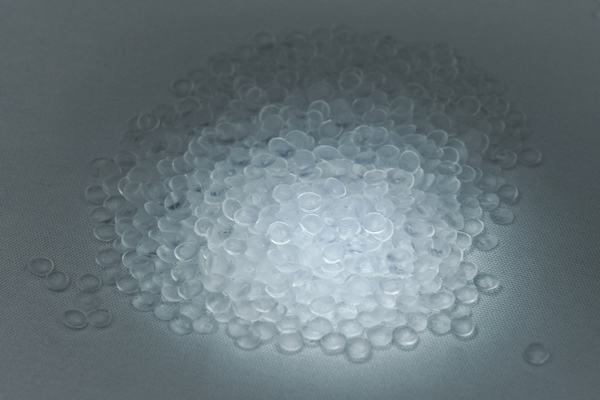
2. Classification and Characteristics of Mainstream Medical Injection Molding Materials
2.1 Thermoplastic Polymers: The Most Widely Used "Workhorses"
-
Polypropylene (PP)
-
Properties: High-temperature resistance (121°C steam sterilization), chemical inertness, low cost.
-
Applications: Disposable syringes, IV bags, Petri dishes, medical packaging.
-
Case Study: A brand’s insulin pen uses modified PP for enhanced impact resistance.
-
Polyethylene (PE)
-
Properties: Low-density (LDPE) for flexibility, high-density (HDPE) for rigidity.
-
Applications: Medical catheters, drug bottles, cryogenic storage containers.
-
Advantage: LDPE suits flexible infusion tubes; HDPE is ideal for chemical-resistant reagent bottles.
-
Polycarbonate (PC)
-
Properties: High transparency, strong impact resistance, heat-resistant (130°C).
-
Applications: Surgical lamp housings, hemodialyzers, endoscope components.
-
Challenge: Special modification is required to reduce bisphenol A (BPA) residues.
-
Polyamide (PA/Nylon)
-
Properties: High strength, wear resistance, fatigue resistance.
-
Applications: Surgical sutures, dental instruments, absorbable stents (e.g., PGA/PLA copolymers).
-
Innovation: Biodegradable nylon reduces secondary surgery risks for temporary implants.
2.2 Thermosetting Polymers: High-Temperature "Special Forces"
-
Epoxy Resin
-
Properties: High-temperature resistance, excellent chemical stability.
-
Applications: Dental restorative materials, medical electronic encapsulation (e.g., pacemaker housings).
-
Limitation: Irrecoverable post-molding, requiring strict process control.
-
Silicone Rubber
-
Properties: Biologically inert, highly flexible, aging-resistant.
-
Applications: Catheter connectors, artificial heart valves, cosmetic implants (e.g., breast prostheses).
-
Advantage: Liquid silicone rubber (LSR) injection molding enables ultra-thin, complex structures.
2.3 High-Performance Engineering Plastics: Pushing Performance Limits
-
Polyetheretherketone (PEEK)
-
Properties: Radiation-resistant, heat-resistant (260°C), mechanical properties comparable to metals.
-
Applications: Spinal fusion cages, cranial repair plates, orthopedic surgical instruments.
-
Case Study: 3D-printed PEEK implants enable personalized orthopedic repairs.
-
Polyphenylene Sulfide (PPS)
-
Properties: Chemical corrosion resistance, high dimensional stability.
-
Applications: Medical analytical instrument parts, sterilization trays.
-
Trend: Carbon fiber-reinforced PPS is used in advanced surgical robot components.
2.4 Biodegradable Materials: The Future of Green Healthcare
-
Polylactic Acid (PLA)
-
Properties: Derived from corn starch, fully degradable into CO₂ and water.
-
Applications: Absorbable sutures, orthopedic fixation pins, drug delivery carriers.
-
Challenge: Toughness enhancement via blending is needed to prevent brittle fracture.
-
Polyhydroxyalkanoates (PHA)
-
Properties: Superior biocompatibility to PLA, adjustable degradation rates.
-
Applications: Tissue engineering scaffolds, eco-friendly medical packaging.
-
Prospect: Combined with 3D printing for personalized medical implants.
3. Key Considerations for Material Selection
-
Product Functionality: Transparency (PC), flexibility (silicone), strength (PEEK).
-
Sterilization Method: Steam sterilization favors PP/PE; ethylene oxide sterilization avoids absorbent materials.
-
Cost and Sustainability: Bio-based materials (e.g., PLA) align with ESG trends but require performance-cost balancing.
-
Regulatory Compliance: Prioritize suppliers with FDA/CE-certified materials.
4. Future Trends: Intelligence and Personalization
-
Composite Materials: Nanofiller reinforcement, integrated conductive materials (e.g., smart sensor implants).
-
4D Printing Materials: Shape-memory polymers for self-expanding vascular stents.
-
Circular Economy: Chemical recycling technologies promote closed-loop medical plastic utilization.
Conclusion
Material selection for medical injection molding is a delicate balance of technology, safety, and cost. With advancements in biomaterials science and manufacturing, future solutions will feature higher performance, biodegradability, and intelligence, driving the medical industry toward safer, more sustainable development. Practitioners must stay updated on material innovations and regulatory dynamics to maintain competitiveness.