In the field of medical injection molding, the precision and efficiency of mold design are directly related to product quality and cost. Below, we delve into the core processes of medical injection mold design, providing reference and inspiration for industry colleagues.
1. Precise Cavity Layout
Cavity layout, the starting point of the design process, involves the rational arrangement of one or more plastic parts based on customer requirements, injection molding processes, and mold structure best practices. This process not only tests a designer's deep understanding of mold structure and plastic processability but also directly impacts the smoothness of subsequent injection molding processes.
When laying out cavities, considerations must be made from two dimensions: injection molding process and mold structure.
-
Injection Molding Process Perspective:
-
Optimize runner length for uniform plastic fill.
-
Minimize runner waste to reduce costs.
-
Select gate locations to ensure balanced feeding and cavity pressure, enhancing product quality.
-
Mold Structure Perspective:
-
Ensure tight sealing to prevent leakage.
-
Fully consider the space requirements for components such as sliders, angles, and cams, ensuring sufficient strength of mold structural parts and no interference between moving parts.
-
Carefully plan the layout of screws, cooling channels, and ejection mechanisms to avoid mutual interference.
-
The overall mold design should be compact, with coordinated length-to-width ratios, taking into account the installation requirements of the injection molding machine.
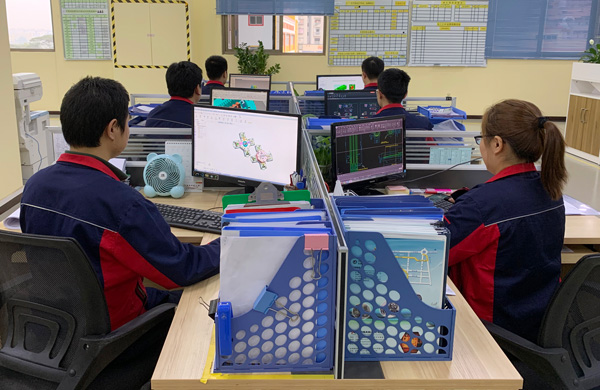
2. Drawing Quotation Diagrams and Precise Material Ordering
-
Quotation Diagram: As the initial mold design plan, the quotation diagram provides a detailed annotation of the mold base, structure, and size of the mold cavity material, serving as a clear reference for material ordering.
-
Material Ordering Process: Based on the quotation diagram, a simplified mold base diagram is drawn, and a material order form is filled out. During this process, appropriate mold materials are selected based on the specific requirements of the mold to ensure performance and longevity.
3. In-depth Design of Mold Structure
The design of the mold structure requires comprehensive consideration of the injection molding machine type, plastic processability, and various technical factors, including but not limited to:
-
Technical specifications of the injection molding machine;
-
Plastic process characteristics;
-
Optimized design of the feeding system (runners, gates, etc.);
-
Precise design of forming components;
-
Selection of commonly used structural components;
-
Flexible design of slider mechanisms;
-
Reliable design of ejection mechanisms;
-
Effective control of mold temperature;
-
Improvement of the ventilation system;
-
Reasonable selection of mold materials.
During the design process, special attention should be given to the following points:
-
3D Layout Deepening: Based on the initial 2D layout, a more in-depth 3D design is carried out to ensure the rationality and practicality of the layout.
-
Mold Splitting Techniques: Select the best parting line, balance lateral pressures, and ensure the perfect integration of product appearance and function.
-
Mold Strength Verification: Comprehensively assess the overall and local strength of the mold, and optimize the structure if necessary to enhance mold durability.
-
Mold Component Design:
-
Forming Components: Such as cavities, cores, inserts, etc., must be easy to process, repair, and assemble, while ensuring the strength and appearance quality of the forming components.
-
Structural Components: Such as locating rings, nozzles, screws, etc., their design and selection need to balance practicality and maintainability.
-
Insert Splitting: Comprehensive consideration should be given to factors such as processability, maintainability, strength, and cooling effects to ensure the rationality of insert design.
-
Ejection Pin and Cooling Channel Layout: Typically, ejection pins are laid out first, followed by cooling channels, but the possibility of subsequent mold modifications must be considered for flexible adjustments.
-
Sleeve Placement: Particularly suitable for forming pillars and deep ribs, it is necessary to ensure reasonable sleeve wall thickness for easy ejection and to avoid bending.
4. Refined Production of Mold Drawings
Mold drawings are the key bridge for translating design intent into physical molds. They must be drawn strictly in accordance with national standards and combined with actual factory practices to ensure the accuracy and readability of the drawings. The drawings include the overall assembly structure diagram, technical requirements, and detailed drawings of all components, providing comprehensive guidance for mold manufacturing.
Through the meticulous design and strict control of these processes, the design of medical injection molds not only meets the functional requirements of products but also ensures production efficiency and cost control, providing solid support for the innovative development of the medical industry.