Medical injection molds are critical tools for producing high-precision medical device components, with their processing quality directly impacting product safety, functionality, and lifespan. Compared to ordinary industrial molds, medical molds must meet stricter standards, particularly in terms of precision, material compatibility, cleanliness, and regulatory compliance. This article explores the four core requirements for medical injection mold processing based on industry needs, helping practitioners grasp key technical points.
1. Precision Manufacturing: Micron-Level Tolerance Control is Vital
Medical products demand near-flawless dimensional accuracy. For example, the piston in an insulin pen must fit seamlessly with the syringe barrel, with tolerances controlled within ±0.005mm. Even a 0.01mm deviation in a cardiac stent’s microstructure could lead to surgical failure. To achieve this:
-
High-precision machining equipment such as five-axis CNC centers and wire-cut EDM machines ensure cavity surface roughness below Ra0.05μm.
-
Advanced inspection technologies like CMM (Coordinate Measuring Machines) and optical projectors monitor critical dimensions in real time, while SPC (Statistical Process Control) reduces tolerance fluctuations to one-third of design specifications.
-
Optimized heat treatment processes, including vacuum quenching and cryogenic treatment, eliminate internal stresses to prevent dimensional shifts during long-term use.
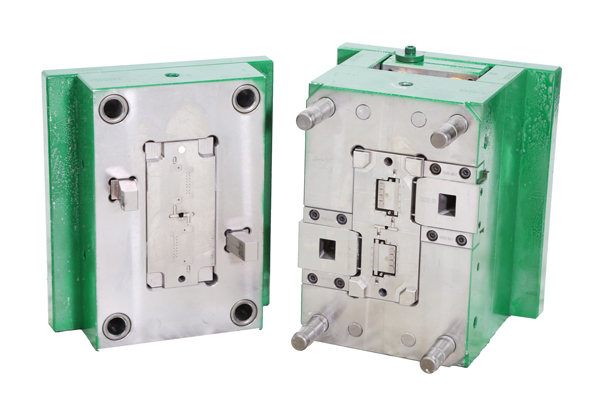
2. Material Selection: Balancing Biocompatibility and Corrosion Resistance
Medical molds directly contact molten medical-grade plastics (e.g., PP, PE, PPSU), requiring materials that ensure both processing performance and product safety:
-
Mold steel grades like S136 and NAK80 stainless steel are preferred for their corrosion resistance, minimizing rust contamination and downtime.
-
Surface treatments such as hard chrome plating, PVD coatings, or nitriding enhance wear resistance and reduce demolding friction.
-
Non-toxic certification: All materials must pass FDA and ISO 10993 biocompatibility tests to ensure no harmful substances are released under high-temperature, high-pressure conditions.
3. Clean Production: Eliminating Contamination Risks from the Source
Medical products, like disposable syringes, require molds processed in Class 10,000 (ISO 8) cleanrooms, adhering to:
-
Dust-free environments: Equipped with air showers and laminar flow hoods, maintaining airborne particle concentrations ≤3,520 particles/m³.
-
Closed-loop machining: Oil mist collectors and central dust extraction systems prevent cutting fluid particles from adhering to mold surfaces.
-
Deburring and polishing: Electropolishing and ultrasonic cleaning remove microscopic defects to avoid metal fragments scratching products.
-
Packaging and transport protocols: Molds are sealed in double-layer cleanroom bags and labeled “Medical Use Only” to prevent cross-contamination.
4. Regulatory Compliance: A Traceable Lifecycle Management System
The medical industry is heavily regulated, requiring molds to maintain comprehensive compliance documentation:
-
Design qualification (DQ): Moldflow simulations analyze gate placement and cooling channel layouts to prevent defects like sink marks or warping.
-
Process qualification (PQ): After 3,000–5,000 production cycles, key dimensions are tested for stability, with CPK reports generated.
-
Document retention: Mold drawings, processing parameters, and inspection records must be stored for at least 15 years to support FDA audits.
-
Change control: Any modifications (e.g., cavity polishing, ejector pin replacements) require revalidation and UDI (Unique Device Identification) updates.
Conclusion: Craftsmanship Safeguards Lives
Medical injection mold processing integrates technology, management, and responsibility. From 0.001mm precision demands to 15-year document retention, every detail impacts patient safety. As technologies like 3D printing and smart sensors evolve, the future of medical molds will prioritize higher precision, shorter lead times, and full traceability. For practitioners, continuous improvement in craftsmanship and strict adherence to compliance are essential for long-term success in the medical sector.