In the production process of medical plastic products, injection molds play a crucial role. They are not only the key components that give plastic products their shape and size, but also process plastic raw materials into various medical devices and precision injection-molded parts that we need in our daily lives through high-temperature injection molding technology. From laryngoscopes, dialysis tubes to Luer connectors, and even connectors that we may come into contact with daily, the production of these products cannot be separated from the precise manufacturing of injection molds. Next, the editor of Yize Mold will provide an in-depth overview and analysis of the overview and composition of medical injection molds in medical plastic products factories.
I. Overview and Considerations for Designing Medical Injection Molds
The design of medical molds not only affects the product's performance and molding effect but also directly impacts production efficiency and cost control. During the design process, we need to pay attention to the following points:
-
Selection of Parting Surface and Gate Location: This should be determined based on the product's performance requirements and molding characteristics to ensure product quality and production efficiency.
-
Manufacturability of the Mold: Consider the equipment status and technical capabilities. The design plan should ensure that the mold, from the overall structure to individual parts, is easy to machine and the dimensional accuracy is easy to guarantee.
-
Injection Production Rate: The number of injections per unit time should be increased as much as possible, and the molding cycle should be shortened to improve production efficiency.
-
Representation of Precision Requirements: The dimensions and structures with precision requirements, such as holes, pins, protrusions, and recesses, should be accurately represented in the mold to reduce the amount of processing after the plastic part is molded.
-
Simplification of Mold Structure: Strive for a simple, practical, stable, and reliable mold structure with a short cycle time and low cost, which is easy to assemble, maintain, and replace worn parts.
-
Selection and Treatment of Mold Materials: Appropriate mold materials should be selected based on product requirements and production environment, and proper treatment should be carried out.
-
Standardized Production of Molds: Standard mold bases, commonly used ejector pins, guide components, and other standard parts should be used as much as possible to improve production efficiency and reduce costs.
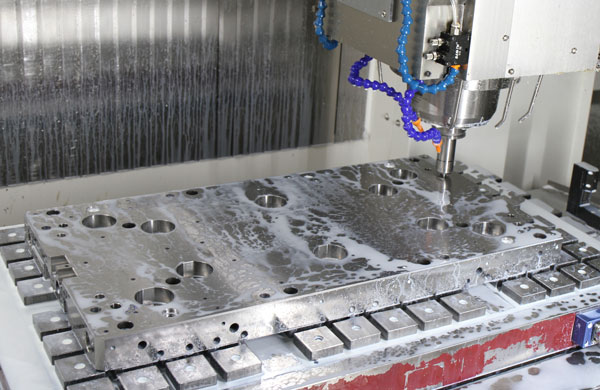
II. Basic Composition of Medical Injection Molds
Medical injection molds consist of multiple systems, each playing an indispensable role:
-
Gating System: This is the channel through which molten material flows from the injection machine nozzle into the mold cavity, including the main runner, branch runners, gates, cold slug wells, and puller rods, ensuring that the material flows into the mold cavity uniformly and smoothly.
-
Molding Parts: Including cores, cavities, and other auxiliary parts, these are the key components for directly molding plastic parts, and their accuracy and shape directly affect the quality of the plastic parts.
-
Temperature Control System: Used to regulate the temperature of the mold to ensure a stable temperature environment during the molding process of the plastic parts, thereby improving product quality and production efficiency.
-
Ejection System for Plastic Parts: Including side-action mechanisms, secondary ejection mechanisms, etc., used to eject the plastic parts from the mold after molding, facilitating demolding and subsequent processing.
-
Mounting Portion: The part that securely mounts the mold body on the injection machine, ensuring the stability and safety of the mold during production.
-
Connection System: Connects the various structural components into a complete mold, ensuring tight connections and coordinated work among the mold components.
-
Guiding System: Such as guide pins and guide slots, used to ensure the accuracy of the relative movement between the structural components, ensuring the precision and stability of the mold during the molding and opening processes.
The above is an overview and detailed composition of medical injection molds in medical plastic products factories. If you want to learn more professional knowledge or have any questions, please feel free to consult us. We will sincerely provide you with professional answers and services.