In the field of injection mold processing, steel molds have long held a dominant position and are widely used by many enterprises. However, in recent years, aluminum molds, as an emerging mold form with low cost and fast production, are gradually coming into people's view. So, can rapid aluminum molds really replace traditional injection steel molds? Before exploring this question, it is necessary for us to first gain an in - depth understanding of the advantages and disadvantages of these two types of injection molds.
I. Steel Molds: The Strengths and Limitations of the Traditional Powerhouse
(1) What are Steel Molds
Injection steel molds are key molds used in the injection molding process, mainly made of steel. Injection molding is a processing method that involves injecting molten plastic material into the mold cavity. After the plastic cools and solidifies, a plastic product with a specific shape is obtained, and injection steel molds play a crucial role in this process. They usually consist of a cavity and a core. The cavity shapes the external appearance of the plastic product, while the core forms the internal shape. During injection mold processing, the plastic melt is injected into the space between the cavity and the core. After cooling and solidification, the desired plastic product is formed.
The manufacturing of injection steel molds involves a series of complex processes, including design, machining, heat treatment, and assembly. Steel has characteristics such as high strength, high hardness, good wear resistance, and corrosion resistance. This enables injection steel molds to withstand the high pressure, high temperature, and friction during the injection molding process, ensuring the precision and service life of the molds. They are widely used in various industries, such as automobile manufacturing, electronics and electrical appliances, medical devices, and toys, for producing various plastic mold - processed products, such as shells, parts, and containers.
(2) Advantages of Injection Steel Molds
-
High Dimensional and Shape Accuracy: They can produce plastic products with very high dimensional accuracy, ensuring the consistency of product dimensions. For example, in the production of electronic device shells, they can precisely control the dimensions of various holes and slots to meet the installation requirements of electronic components. They can also achieve the injection molding of complex shapes. For products with fine structures and curved surfaces, such as automotive interior parts and toys, they can accurately replicate the shape of the mold.
-
Strong Durability: Steel has high hardness and can withstand the high pressure and friction during the injection molding process, making it less prone to deformation and wear. This allows injection steel molds to maintain stable performance during long - term production, greatly extending their service life. The service life of steel molds can reach 300,000 - 1,000,000 cycles.
-
Good Corrosion Resistance: For products that require the use of special plastic materials or are produced in harsh environments, the corrosion resistance of injection steel molds can ensure that the molds are not eroded by chemical substances, ensuring the smooth progress of production. For example, when producing chemical containers and other products, steel molds can withstand the influence of corrosive plastic materials.
-
High Production Efficiency and Short Molding Cycle: Due to the good thermal conductivity of steel molds, they can quickly transfer the heat of the plastic melt, speed up the cooling process, and thus shorten the molding cycle. For large - scale production, this can significantly improve production efficiency and reduce production costs. Moreover, their durability allows for long - term continuous production without the need for frequent mold changes. This not only improves production efficiency but also reduces downtime and production interruptions caused by mold changes.
-
Wide Adaptability: They can be used for injection molding various types of plastic raw materials, including engineering plastics and general - purpose plastics. Whether it is plastic with high hardness or plastic with special properties, injection steel molds can meet the production requirements. They can also adapt to different product requirements. Whether it is small precision parts or large plastic products, injection steel molds can be designed and manufactured according to the product requirements. They can adapt to different product sizes, shapes, and complexities, providing flexible solutions for production in various industries.
(3) Disadvantages of Injection Steel Molds
-
Long Production Cycle: Generally, the production cycle of steel molds is 30 - 35 days.
-
High Cost: The price of steel molds generally ranges from tens of thousands to hundreds of thousands of yuan per set.
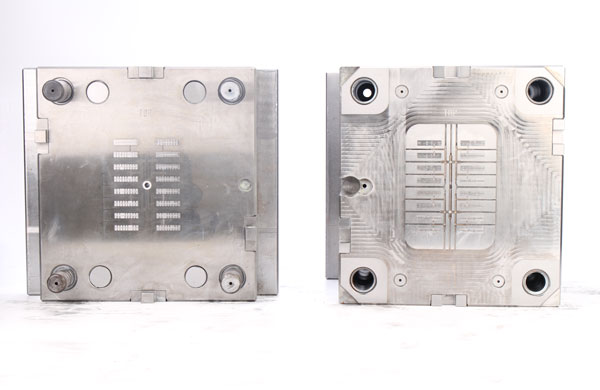
II. Aluminum Molds: The Opportunities and Challenges of the Emerging Force
(1) Material Characteristics
The main material of injection aluminum molds is aluminum alloy.
(2) Advantages of Aluminum Molds
-
Relatively Low Cost: Compared with steel molds, the manufacturing cost of injection aluminum molds is lower, especially for small - batch production or products with rapid product updates, which offers more economic advantages.
-
Short Processing Cycle: Aluminum alloy has good machinability, which allows for the rapid manufacture of molds with complex shapes, shortening the mold development cycle.
-
Easy to Modify: If the design of the plastic product needs to be modified, injection aluminum molds are easier to machine and adjust.
(3) Disadvantages of Aluminum Molds
-
Relatively Short Service Life: Although aluminum alloy has certain hardness and wear resistance, compared with steel molds, the service life of injection aluminum molds is relatively short, generally around 50,000 cycles.
-
Limited Pressure - Bearing Capacity: During the injection molding process, the pressure that injection aluminum molds can withstand is relatively small, which may not be suitable for the production of large or high - strength plastic products.
III. Comprehensive Comparison and Conclusion
Based on the above analysis, we can see that aluminum molds and steel molds each have their own applicable scenarios. Aluminum molds are suitable for new products with small quantities and low product requirements, especially in the trial - production and verification stage of new product development. Enterprises can decide whether to continue the project investment based on market feedback. Steel molds, on the other hand, are suitable for injection molding with high precision requirements and large production volumes.
Therefore, from the current situation, aluminum molds cannot completely replace steel molds. They play their respective roles in different production needs. Enterprises should reasonably choose the appropriate mold type based on factors such as their own production scale, product requirements, and cost budget to achieve the best production benefits.