In the flourishing medical industry, medical injection mold processing holds a pivotal position. It acts like a "behind - the - scenes craftsman" in the medical field, widely applied in various crucial areas such as medical devices and medical consumables, providing solid support for the progress of the medical industry. However, in the actual processing process, numerous thorny problems are often encountered. These problems not only affect the quality and production efficiency of the molds but may also lead to defects in the products, thereby increasing production costs. Therefore, having an in - depth understanding of the common problems in medical injection mold processing and their solutions is of crucial significance for improving the mold manufacturing level and product quality.
I. Mold Design Problems and Solutions
(1) Dimensional Accuracy Deviation
-
Cause Analysis: Misunderstandings of product dimensions during the design phase, improper setting or operation of software accuracy, and a lack of in - depth understanding of mold structure and processing technology can all lead to dimensional accuracy deviation.
-
Influencing Factors: Product material characteristics, the complexity of the mold structure, and the experience and skills of the designers all have an impact on dimensional accuracy.
-
Preventive Measures: Accurately calculate the shrinkage rate and make compensations, select appropriate software and ensure that designers are proficient in its operation, and strengthen communication and collaboration between designers and process personnel to reduce the occurrence of dimensional accuracy deviation from the source.
-
Solutions: If the dimensional deviation is small, it can be corrected by adjusting the processing parameters; if the deviation is large, the mold needs to be repaired or re - processed.
(2) Unreasonable Structure
-
Cause Analysis: Insufficient analysis of product forming and demolding requirements, lack of innovation, and blind adherence to traditional designs can all result in an unreasonable mold structure.
-
Influencing Factors: Product shape and structure, forming process, manufacturing cost, and cycle are interwoven factors that jointly affect the rationality of the mold structure.
-
Preventive Measures: Conduct in - depth analysis of product characteristics and optimize the design scheme; draw on advanced design concepts and successful cases; organize design reviews to ensure the scientific and reasonable structure of the mold.
-
Solutions: For demolding difficulties, increase the draft angle or use a release agent; for runner and gate problems, re - design is required; if the problem is serious, the mold needs to be re - designed and manufactured.
II. Processing Technology Problems and Solutions
(1) Cutting Processing Errors
-
Cause Analysis: Tool wear, improper cutting parameters, insufficient precision and stability of the machine tool, unreasonable process routes, and uneven workpiece materials can all trigger cutting processing errors.
-
Influencing Factors: Tool material quality, the degree of optimization of cutting parameters, machine tool performance maintenance, and workpiece material characteristics all affect the accuracy of cutting processing.
-
Preventive Measures: Regularly replace tools, reasonably select and optimize cutting parameters, strengthen the maintenance of machine tools, and formulate scientific and reasonable process routes.
-
Solutions: For errors caused by tool wear, compensation correction can be used; if the error is large, re - processing or repair of the mold is required; for surface roughness problems, adjust the cutting parameters or conduct subsequent processing.
(2) EDM Defects
-
Cause Analysis: Unreasonable discharge parameters, improper design and manufacture of electrodes, and poor circulation and filtration of the working fluid can all lead to EDM defects.
-
Influencing Factors: Discharge parameters, electrode quality and precision, and the working fluid performance and circulation system jointly determine the quality of EDM.
-
Preventive Measures: Reasonably set discharge parameters, manufacture electrodes with high precision, and regularly inspect and replace the working fluid to ensure a stable and reliable EDM process.
-
Solutions: For surface burns, polishing can be carried out; if the discharge marks are deep, the electrode needs to be repaired or re - processed; if the discharge is unstable, check and adjust the discharge parameters and the working fluid system.
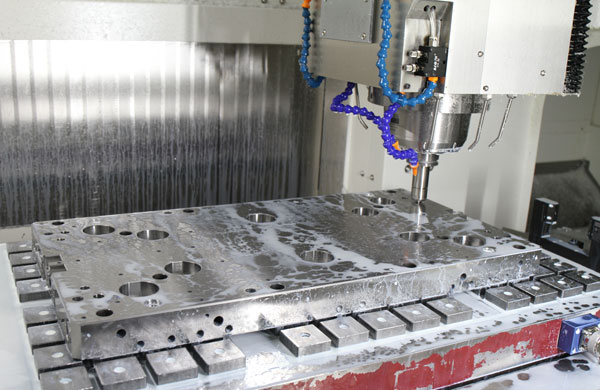
III. Material Selection Problems and Solutions
(1) Mismatched Material Performance
-
Cause Analysis: Insufficient understanding of the product's use and working environment, and failure to conduct strict acceptance inspections during procurement can both lead to mismatched material performance.
-
Influencing Factors: Product use conditions, mold life requirements, and the supplier's reputation and quality control level all affect material selection.
-
Preventive Measures: Select appropriate materials by fully considering the product's use environment, establish strict procurement standards and acceptance systems, and cooperate with reliable suppliers.
-
Solutions: If the material has not been used, it can be replaced with a suitable one; if the material has been used, its performance can be improved through surface treatment.
(2) Unstable Material Quality
-
Cause Analysis: Unstable production processes of suppliers, effects on material transportation and storage, and imperfect enterprise inspection methods can all lead to unstable material quality.
-
Influencing Factors: The supplier's management level, transportation and storage conditions, and the enterprise's inspection capabilities all have a significant impact on material quality.
-
Preventive Measures: Conduct a comprehensive evaluation and management of suppliers, optimize material transportation and storage conditions, and improve the enterprise's inspection equipment and processes.
-
Solutions: Communicate with suppliers to improve their production processes; return or replace unqualified materials; and strengthen quality monitoring during production.
IV. Assembly and Debugging Problems and Solutions
(1) Poor Part Fit
-
Cause Analysis: The machining accuracy of parts does not meet the requirements, the assembly process is unreasonable, and the parts are not cleaned and trimmed can all lead to poor part fit.
-
Influencing Factors: Part machining accuracy, the rationality of the assembly process, and the skills and operation specifications of the assembly personnel all affect the fitting effect of the parts.
-
Preventive Measures: Improve the machining accuracy of parts, formulate reasonable assembly processes and train assembly personnel, and clean and inspect the parts before assembly.
-
Solutions: For parts with poor fit, grinding and polishing can be carried out; if the problem is serious, re - processing or adjustment of the assembly process is required; during the debugging process, adjust the assembly accuracy according to the forming situation.
(2) Unreasonable Debugging Parameters
-
Cause Analysis: Insufficient understanding of injection molding process parameters, failure to fully consider the influence of multiple factors, and subjective judgment during debugging can all lead to unreasonable debugging parameters.
-
Influencing Factors: Mold structure and size, product material shape, injection molding machine performance parameters, and the experience and skills of the debugging personnel all affect the debugging parameters.
-
Preventive Measures: Debugging personnel should be familiar with parameter settings and skills, analyze and determine preliminary parameters before debugging, and use scientific experiments to optimize the parameters.
-
Solutions: Adjust the injection molding process parameters according to the types of product defects and continuously optimize by observing the forming situation until the best effect is achieved.
V. Conclusion
In summary, medical injection mold processing holds an irreplaceable and significant position in modern manufacturing, but problems may occur in various links such as mold design, processing technology, material selection, and assembly and debugging. By conducting an in - depth analysis of these common problems and their corresponding solutions, we can more calmly deal with various challenges in actual operations, effectively improve mold quality and production efficiency, ensure product quality, and inject powerful impetus into the booming development of the medical injection mold processing industry.
Dongguan Yize Mold Co., Ltd. focuses on the field of medical injection mold processing and has many years of experience in the design and manufacture of precision molds and the production of precision injection - molded products. The company is headquartered in Dongguan, the manufacturing capital, with convenient transportation and logistics. We provide a complete set of solutions from product design, precision mold manufacturing, injection molding and assembly to after - sales service for products such as automotive connectors, medical product injection molding, dust - free injection molding, and PFA custom injection molding. Welcome to inquire. Contact number: +86 13302615729 (also available on WeChat and Whatsapp).
In the flourishing medical industry, medical injection mold processing holds a pivotal position. It acts like a "behind - the - scenes craftsman" in the medical field, widely applied in various crucial areas such as medical devices and medical consumables, providing solid support for the progress of the medical industry. However, in the actual processing process, numerous thorny problems are often encountered. These problems not only affect the quality and production efficiency of the molds but may also lead to defects in the products, thereby increasing production costs. Therefore, having an in - depth understanding of the common problems in medical injection mold processing and their solutions is of crucial significance for improving the mold manufacturing level and product quality.