Introduction
In today's various industries, medical devices play an indispensable role, and the injection molding of their housings is a crucial link. A good injection - molding process can ensure the precision, strength, and aesthetics of the housing, directly affecting the performance and user experience of medical devices. However, there are many difficulties in this process. This article will conduct an in - depth analysis of these difficulties and explore effective solutions.
Difficulties and Solutions in Material Selection and Performance Balance
1. Difficulties
1.1 Material Matching Challenge
Plastic materials are diverse, each with its own physical and chemical properties, such as strength, toughness, weather resistance, and transparency. When selecting materials for medical device housings, it is necessary to meet basic functions such as protecting internal components and facilitating hand - held operation while controlling costs. Choosing the right material is quite challenging.
1.2 Complex Performance Evaluation
Accurately evaluating the performance of different materials under actual working conditions requires a large amount of test data and rich practical experience. In addition, full consideration must be given to the compatibility between the material and the internal components of the medical device to avoid damage or performance degradation of the components due to chemical or physical reactions.
2. Solutions
2.1 In - depth Understanding of Material Properties
-
Analysis of Common Materials:
-
ABS: It has good overall physical properties, with excellent strength and toughness, good processability, moderate requirements for temperature and pressure, and relatively low cost. It can effectively protect components and is suitable for injection molding production.
-
PC: It has outstanding impact resistance and high transparency, but requires high processing temperatures and is relatively expensive. When applying, a balance between performance and cost needs to be considered.
2.2 Comprehensive Consideration of Multiple Factors for Material Selection
-
Performance Demand Matching:
-
Analyze the usage scenarios of medical devices. For devices prone to collisions, materials with good strength and toughness (such as ABS or modified materials) should be selected.
-
Consider special performance requirements. For devices with electrostatic - sensitive components, anti - static materials (such as anti - static ABS or materials with anti - static additives) should be chosen.
-
Cost Factor Weighing:
-
Comprehensively evaluate factors such as material purchase price, processing cost, rejection rate, and material utilization rate. Different materials have different processing requirements, which affect energy consumption and other costs; a high rejection rate will increase the unit cost; and the difficulty of waste recycling should also be considered.
-
Compatibility Assurance:
-
Sort out and analyze the characteristics of the internal components of medical devices. Refer to relevant data or conduct tests to ensure that the selected material has no chemical reactions or adverse physical interactions with the components, such as corrosion resistance and matching thermal expansion coefficients.
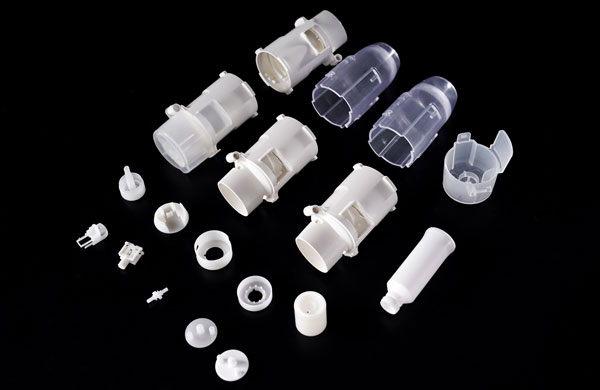
Difficulties and Solutions in Mold Design and Manufacturing Precision
1. Difficulties
1.1 Design Adaptation Challenge
Medical device housings come in various shapes, and precise installation spaces need to be reserved inside for components such as batteries, circuit boards, and displays. If the mold design is unreasonable, the injected housing may not fit well with the internal components, leading to problems such as difficult assembly, loose components, or even component damage.
1.2 Manufacturing Precision Challenge
It is difficult to achieve high - precision dimensional control during the mold manufacturing process. Small dimensional deviations can affect the appearance quality of the housing, such as surface unevenness and excessive gaps, and also have a negative impact on its function, such as reducing the stability of component installation. Achieving high - precision manufacturing relies on advanced equipment and good processes, which often come with high costs and technical thresholds.
1.3 Complexity of Demolding Design
Designing a mold that can meet the complex shape and internal structure requirements of the housing while ensuring effective demolding is challenging. Different housing structures may require special demolding mechanisms, such as side ejection or oblique ejection. If the demolding method is not well - designed, the formed housing may be difficult to smoothly remove from the mold, which may lead to housing damage or low production efficiency.
2. Solutions
2.1 Following Mold Design Principles
-
Shape and Size Matching:
-
The shape of the mold cavity must strictly correspond to the outer contour of the medical device housing, and the dimensional tolerance of the cavity should be strictly controlled to ensure the dimensional precision of the housing and enable accurate assembly with internal components. For example, for a specific hand - held medical device housing, the key dimensional tolerance of the mold cavity can be controlled within ±0.1mm.
-
Reserve sufficient and reasonable installation spaces for internal components and design structures such as grooves and positioning holes to facilitate the installation and fixation of components in the housing.
2.2 Adopting High - Precision Manufacturing Methods
-
Use of Advanced Equipment:
-
Use CNC machining centers for rough and finish machining of molds. By precisely controlling the tool path, high - precision dimensional machining can be achieved.
-
For complex mold structures, combine special processing methods such as electrical discharge machining to complete parts that are difficult to achieve with conventional processing.
-
Quality Monitoring and Assurance:
-
Regularly calibrate and maintain the processing equipment to ensure the stability of its processing precision.
-
Use precision measuring equipment such as coordinate measuring machines to conduct real - time measurement and feedback of key mold dimensions, and promptly identify and correct dimensional deviations.
Quality Control and Defect Prevention
1. Difficulties
1.1 Significant Impact of Common Defects
Common quality defects in injection - molded products, such as bubbles, silver streaks, shrinkage, and flash, are prone to occur in medical device housing injection molding. These defects not only affect the appearance quality of the housing but also reduce its mechanical properties and functional reliability, leading to product non - conformity, increased rejection rates, and production costs.
1.2 Difficulty in Controlling Defect Causes
It is difficult to accurately identify the causes of various quality defects and take effective preventive measures. Different defects may be caused by multiple factors. A thorough understanding of all aspects of the injection - molding process, such as raw material handling, mold design, and injection - molding operation, is required to prevent defects from the source.
2. Solutions
2.1 In - depth Analysis of Defect Causes and Preventive Measures
-
Bubbles:
-
Causes: The raw material is not sufficiently dried, and the water vaporizes during injection molding to form bubbles. Poor exhaust during the injection - molding process prevents air from being discharged in time and is wrapped by the molten plastic to form bubbles. Excessive injection speed causes turbulence in the molten plastic in the cavity,卷入 air to form bubbles.
-
Preventive Measures: Strengthen the drying treatment of raw materials to ensure that the moisture content is below the specified value; set exhaust grooves on the mold; and reasonably adjust the injection speed.
-
Silver Streaks:
-
Causes: The impurity content in the raw material is too high, and it is not evenly mixed with the molten plastic, resulting in silver streaks. Improper temperature control, such as too high a barrel temperature or too low a mold temperature, causes changes in the state of the molten plastic and produces silver streaks.
-
Preventive Measures: Strictly screen the raw materials to remove impurities; precisely control the barrel temperature and mold temperature, and set appropriate temperature ranges according to different materials and mold structures.
-
Shrinkage:
-
Causes: Insufficient holding pressure or too short holding time prevents the plastic from being fully compensated during the cooling and shrinking process, resulting in depressions on the surface of the housing.
-
Preventive Measures: Set the holding pressure and holding time reasonably according to the wall thickness of the housing and the shrinkage rate of the plastic raw material.
-
Flash:
-
Causes: Insufficient mold clamping force allows the plastic to overflow the mold cavity during injection molding, forming excess plastic. Unreasonable design of the mold parting surface makes it easy for plastic to accumulate at the parting surface, forming excess plastic.
-
Preventive Measures: Ensure sufficient mold clamping force. Calculate the appropriate clamping force according to factors such as mold size and injection pressure and regularly check it; optimize the design of the mold parting surface and adopt appropriate sealing measures to prevent plastic accumulation.
Conclusion
In summary, although medical device housing injection molding is of great importance in various industries, it faces difficulties such as material selection, mold manufacturing precision, process parameter optimization, quality control, and cost control. Through in - depth analysis of these problems and the corresponding solutions, it is hoped that relevant practitioners can effectively cope with these challenges, improve the product quality of medical device housings, enhance market competitiveness, and promote the sustainable development of the entire medical industry.