Medical laryngoscopes, as indispensable auxiliary tools in clinical diagnosis and treatment, require careful material selection during injection molding production to ensure product safety, functionality, and service life. This article combines industry practices with principles of materials science to systematically elaborate on the core considerations and implementation strategies for material selection in medical laryngoscope injection molding.
I. Core Material Selection Criteria
-
Biocompatibility Certification
Medical-grade materials must pass tests under the ISO 10993 series standards, covering cytotoxicity, sensitization, genotoxicity, and other items. For example, polypropylene (PP) is widely used in products like syringes that directly contact bodily fluids due to its non-toxic and odorless properties, while polyetheretherketone (PEEK) is preferred for implantable devices due to its biological inertness. Special attention must be paid to the long-term interaction between materials and human tissues to avoid immune rejection or inflammatory reactions.
-
Physical and Mechanical Performance Adaptation
Laryngoscopes must withstand frequent sterilization and mechanical stresses during clinical operations. Therefore, materials need to possess:
-
Balanced Strength and Toughness: For instance, RANPELEN J-560M random copolymer PP has a flexural modulus of 1180 MPa and maintains an Izod impact strength of 29 J/m at -10°C, ensuring resistance to impact in low-temperature environments.
-
High-Temperature Resistance: Materials must withstand steam sterilization at temperatures above 121°C. For example, polysulfone (PPSU) can operate continuously at temperatures up to 180°C, meeting the requirements for multiple sterilizations.
-
Dimensional Stability: Precision components require controlled thermal expansion coefficients to avoid changes in fit gaps due to temperature variations.
-
Process Compatibility
Materials must align with the requirements of precision injection molding:
-
Flowability: The melt mass-flow rate (MFR) should match the complexity of the mold structure. For example, RANPELEN J-560M has an MFR of 18 g/10min at 230°C and a 2.16 kg load, suitable for thin-walled part injection molding.
-
Shrinkage Rate Control: Batch-to-batch material shrinkage rate differences should be ≤0.5%, achieved through mold temperature compensation (80-120°C) and packing pressure adjustment.
-
Demolding Performance: Medical-grade mold release agents and optimized mold parting surface designs are used to reduce flash generation.
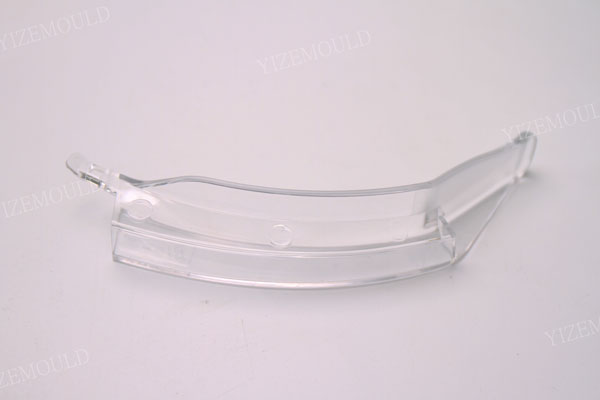
II. Implementation Strategies for Material Selection
-
Standardized Material Library Construction
Establish a performance database covering materials such as PP, PC, and PPSU, clarifying their applicable scenarios:
-
PP: Suitable for non-implantable disposable laryngoscope components, offering low cost and excellent processing performance.
-
PC: Used for transparent observation windows, combining high transparency with impact resistance.
-
PPSU: A premium material for laryngoscope bodies, meeting long-term sterilization and complex usage environment requirements.
-
Supplier Quality Control
-
Raw Material Traceability: Require suppliers to provide original material certificates and DMF registration numbers to ensure material compliance.
-
Batch Consistency: Detect molecular weight distribution through spectral analysis to control shrinkage rate fluctuations.
-
Biocompatibility Verification: Commission third-party institutions for tests such as acute systemic toxicity and intradermal reactions.
-
Process Validation and Optimization
-
Mold Trial Stage: Adjust barrel temperature (PC: 280-320°C), injection speed, and packing time to eliminate defects such as bubbles and sink marks.
-
Annealing Treatment: Perform annealing at 50-60°C for 1-2 hours on PC and other materials prone to internal stress to reduce cracking risks.
-
Clean Production: Manufacture in Class 10,000 cleanrooms and use high-temperature, high-pressure steam sterilization for molds to avoid microbial contamination.
III. Case Study: Application Practice of RANPELEN J-560M
A laryngoscope manufacturer adopted RANPELEN J-560M random copolymer PP and achieved quality improvements through the following measures:
-
Mold Optimization: Designed a hot runner system to reduce gate marks and used S136H stainless steel molds for enhanced corrosion resistance.
-
Process Parameters: Set barrel temperature at 240°C, mold temperature at 60°C, injection pressure at 1500 bar, and packing time at 8 seconds to achieve a tolerance of ±0.02 mm.
-
Quality Control: Conducted dimensional measurements, gamma sterilization compatibility tests, and -10°C low-temperature impact tests for each batch.
IV. Future Trends and Challenges
With the development of minimally invasive surgery and portable devices, medical laryngoscope materials need to evolve in the following directions:
-
Lightweighting: Develop high-modulus, low-density composite materials to reduce the burden on doctors during operation.
-
Functional Integration: Embed sensors or conductive circuits during injection molding to achieve intelligent monitoring.
-
Sustainability: Promote biodegradable polylactic acid (PLA) materials to reduce medical waste pollution.
Conclusion
Material selection for medical laryngoscope injection molding should prioritize safety while balancing functionality and cost-effectiveness. By establishing standardized material systems, strengthening supplier control, and optimizing injection molding processes, product quality and production efficiency can be effectively improved. In the future, with advances in materials science and manufacturing technology, medical laryngoscopes will evolve toward greater precision, intelligence, and environmental sustainability.