Medical device housings, as precision components directly in contact with the human body, have their injection molding quality directly impacting product safety and functionality. Short shot, one of the most common defects in injection molding, often manifests as incomplete cavity filling, incomplete product edges, or local cavities. This article systematically analyzes the root causes of short shots in medical device housing injection molding, considering the process characteristics of this field, and proposes targeted solutions.
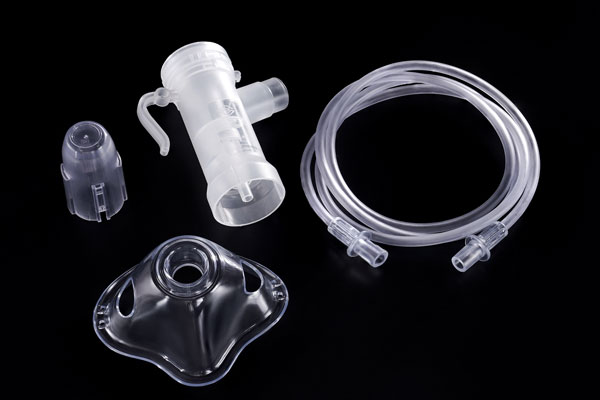
I. Core Causes of Short Shots in Medical Device Housings
-
Mold Design Defects
-
Improper Runner System: Medical device housings often feature complex curved or thin-walled structures. If the main runner diameter is insufficient or the runner length is excessive, melt pressure losses can exceed 30%.
-
Venting System Failure: Medical device housings typically use high-precision molds. If vent slots are less than 0.02mm deep or blocked by oil contamination, trapped air pressures can exceed 15MPa, directly obstructing melt flow.
-
Wall Thickness Imbalance: Medical device housings must balance strength and lightweight design, but abrupt wall thickness changes (e.g., from 2mm to 0.8mm) can cause premature cooling of the melt front.
-
Material Performance Fluctuations
-
Flow Property Differences: Medical-grade PC materials require a stable melt flow index (MFI) of 15–20 g/10min (300°C/1.2kg). If batch-to-batch MFI fluctuations exceed 15%, injection pressure adjustments of 10–20% are necessary.
-
Additive Effects: Medical-grade PPS reinforced with 30% glass fiber has a viscosity 200% higher than neat resin, requiring optimization of screw speed to 40–60 rpm to avoid shear heating.
-
Improper Preprocessing: PA66 and other hygroscopic materials with moisture content exceeding 0.2% can cause vapor expansion of up to 1600 times during melting, leading to sudden pressure drops in the cavity.
-
Process Parameter Out of Control
-
Temperature Management Failure: Temperature deviations of ±10°C in the barrel can change PC material viscosity by 40%. A ventilator housing experienced short shots due to an underheated third zone of the barrel.
-
Packing Phase Defects: Insufficient packing pressure (<60% of injection pressure) or short packing time (<gate solidification time) can increase shrinkage by 1.5–2.0 times.
-
Equipment Malfunctions
-
Insufficient Plasticizing Capacity: The actual plasticizing capacity of the injection molding machine should exceed the part weight by 120%.
-
Worn Sealing Systems: When the clearance between the screw check ring and barrel exceeds 0.1 mm, melt backflow can reach 8–12%.
-
Temperature Control System Failure: Poor thermocouple contact or PID parameter misalignment can cause mold temperature fluctuations of ±8°C.
II. Systematic Solutions
-
Mold Optimization Strategies
-
Runner System Upgrade: Use Moldflow software for simulation and optimization.
-
Venting System Strengthening: Install vacuum venting devices.
-
Wall Thickness Uniformization: Apply topological optimization.
-
Material and Process Synergy Control
-
Material Database Establishment: Record MFI, moisture content, and other parameters.
-
Three-Stage Injection Control: Breakthrough phase (10–20% Vmax), high-speed filling phase (80–100% Vmax), and deceleration phase (30–50% Vmax).
-
Intelligent Packing System: Use pressure sensors for real-time cavity pressure monitoring.
-
Equipment Preventive Maintenance
-
Precision Machining Guarantee: Control cold runner diameter tolerance within ±0.05 mm.
-
Sealing System Repair: Restore screw component clearances to 0.03–0.05 mm using laser cladding.
-
Dual PID Temperature Control: Set independent temperature circuits for the gate area.
III. Implementation Path and Benefit Evaluation
-
DFM Review System: Introduce mold flow analysis during product design.
-
SPC Process Control: Implement process capability control (CPK ≥ 1.33) for key parameters.
-
Knowledge Management System: Digitize defect cases and solutions to form an AI diagnostic model.
By systematically implementing these measures, the short shot defect rate in medical device housing injection molding can be reduced from the industry average of 3–5% to below 0.3%, while production efficiency is improved by 25–35% and the product defect rate is reduced to below 0.5%. In practice, fine-tuning parameters based on specific product characteristics and establishing a continuous improvement mechanism are essential to meet the stringent quality requirements of the medical industry.
Dongguan Yize Mould Co., Ltd. was founded in 2007, is headquartered in the manufacturing capital of Dongguan, convenient transportation and logistics, is engaged in many years in the design and manufacture of precision molds and precision medical injection moulding products manufacturer, the company focuses on the automotive connectors, medical products medical injection moulding, dust-free plastic medical injection moulding, custom medical injection moulding of PFA products such as design, precision mold manufacturing, medical injection moulding and assembly, after-sales service as a whole set of solutions. You can contact us via Email info@yizemould.com or WhatsApp +86 13302615729 !